What is Lithium Polymer Battery
LiPo batteries, short for Lithium Polymer batteries, are a type of rechargeable battery that has taken the electric RC world by storm, especially for planes, helicopters, and multi-rotor/drones.
They are the main reason an electric flight is now a very viable option over fuel-powered models.
LiPo batteries have five main things going for them that make them the optimum battery choice for RC planes and even more so for RC helicopters over conventional rechargeable battery types such as NiCad, or NiMH.
RC Li-Po Battery Pros
LiPo batteries are lightweight and can be made in almost any shape and size.
LiPo batteries have large capacities, meaning they hold lots of energy in a small package (high energy density).
LiPo’s are very good at maintaining a consistent voltage/power output as they discharge. The voltage/power drop however when they are reaching a fully discharged state is very fast (and damaging) when compared to NiCad, NiMH, or PB.
LiPo batteries have high discharge rates to power the most demanding electric RC aircraft and vehicles. LiPo’s also allowed for fairly high charge rates so recharging in an hour or less is possible.
Unlike NiCad or NiMh; LiPo’s have no “memory effect”.
In short, Li-Po cells provide high energy storage density to weight ratios. They also give us a consistent voltage output, are capable of safe fast discharges, have quick recharge times, and can be configured in an endless variety of voltages, capacities, shapes, and sizes.
These benefits are important in any RC model, but for airplanes, helicopters, and quad/multi-rotor they are the reason electric flight has become so popular.
Face it, electric RC cars and RC Boats have been around for decades, but it wasn’t until LiPo battery technology arrived on the scene that electric planes, helicopters, and quad/multi-rotor started showing up and are now surpassing gas, turbine, and even nitro in terms of power to weight ratios.
Why is the power to weigh more critical with RC aircraft? Because it simply takes way more power to get something airborne. Overcoming gravity uses substantial energy over something that drives on wheels or floats on water.
There are a few downsides with LiPo batteries, however; once again proves there is no perfect RC power solution (yet).
RC Li-Po Battery Cons
LiPo batteries are expensive compared to NiCad and NiMH. They have come down in price over the past several years, but are still quite costly.
Although getting better, LiPo’s don’t have very long lifespans when used in high-demand applications like RC flight; perhaps only 100-300 charge cycles (much less if not cared for properly). The harder they are pushed, the shorter their life expectancy. If used gently however in low load applications (TX & RX battery packs for example), they can easily last well over 500 cycles.
Safety issues – because of the high energy density storage coupled with the volatile electrolyte used in LiPo’s, they can burst and/or catch fire when mistreated.
Because of this fire danger, RC LiPo‘s are classified as dangerous goods now by most shipping facilities worldwide making shipping difficult, expensive, or even impossible for all but the smallest capacity LiPos.
LiPo batteries require unique and proper care if they are going to last for any length of time more so than any other battery technology used in RC. Charging, discharging, storage, and temperature all affect the lifespan – get it wrong and a LiPo is a garbage in as little as one mistake!
Before I start talking about the actual care & ratings of LiPo RC batteries, I thought I should go over the basics first.
Feel free to skip down the page if you don’t care about the actual makeup of a lithium polymer battery and just want to know what to look for when buying them, how to properly care for them, and get the most possible life expectancy out of them.
RC LiPo Battery Construction
Almost every RC LiPo battery cell is packaged in a flexible plastic pouch, coincidentally called a “pouch cell”.
The picture to the right shows both a single pouch cell, along with three of the cells combined to create a typical 3 cell (3S) LiPo RC battery pack.
Pouch cells are the perfect solution for building multi-celled battery packs because the flat pouch cell can be stacked with no wasted air spaces like found within round celled battery packs.
Since LiPo’s use, this lightweight plastic pouch instead of a metal can, less weight is the result making pouch called LiPo’s the preferred choice in weight-conscious RC aircraft applications.
By contrast, heavier canned lithium cells such as the very popular Li-Ion 18650 cells that are used in everything from cordless power tools, to Tesla Motor’s current battery packs, weigh in at 20% or more than similar capacity LiPo pouch cells.
These LiPo pouch cells also allow for more thermal expansion and even gassing (electrolyte decomposition) due to the flexible pouch over a metal can that most Li-Ion cells are encapsulated. So, they can also be considered as a safety feature to some extent.
LiPo Battery Internal Structure
If you ever open up a LiPo pouch cell, this is what you’ll find.
A long piece of very thin white plastic microporous film (the polymer), with the thin lithium carbon-coated aluminum & copper anode & cathode electrodes laminated in an alternating pattern on the front and backside of the polymer separator film.
This long film (over 7 feet long in the case of this 5000 mAh cell), is folded accordion-style back and forth upon itself resulting in an alternating anode/cathode stacking with the continuous thin layer of polymer separator sandwiched between them.
This entire folded cell matrix is placed & sealed into the soft plastic pouch, and will be saturated with a greasy/gel-like solvent-based lithium-ion infused organic electrolyte; which incidentally has a very sweet solvent smell much like nail polish remover/acetone.
If you ever smell that unmistakable sweet solvent-like odor from a lipo battery pack, it has a leaking cell and should not be used under any circumstance!
Before the final heat sealing of the pouch, it is pressed under a fair amount of pressure to ensure maximum contact is obtained between the polymer separator film and the anodes and cathodes. The tighter this lamination between layers is, the better the ion transfer efficiency and lower the internal resistance of the battery.
This pressing of the cell just before final sealing also removes any remaining air within the cell. Low humidity & cleanroom manufacturing environments are also very important which adds to the manufacturing costs of lithium batteries.
If you’re wondering what the burnt hole is in the center of all the plates, I purposely drove a nail through this cell to discharge it rapidly & watch the fireworks. The cell rapidly ballooned out, burst, and vented oxygen & flammable electrolyte but never caught on fire.
On the positive side, if it would have burst into flame, I wouldn’t have this picture to show the “guts”. I only did this because I dropped this heavy 6S 5000mAh LiPo pack on the hard concrete floor (yes – very dumb & costly butter finger moment) and one cell was damaged in the process. Lesson learned, don’t carry more LiPo’s than you can safely hold!
Here’s an interesting video of the processes involved in manufacturing LiPo cells & packs.
Hard Case vs Soft Case RC LiPo Batteries
As shown in that manufacturing video above and in the photo below; hard case LiPo‘s use a hard plastic shell to house the soft plastic LiPo pouch cells of the battery pack.
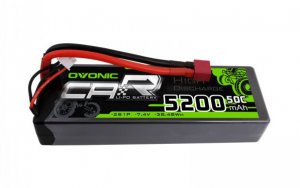
This gives them added protection from moderate impacts and rough use that often occurs with ground RC vehicles such as cars and trucks; where saving weight is a secondary concern over that of protection.
Naturally, this is vehicle-dependent as some RC cars and trucks offer good physical battery protection. This is also application-dependent; racing with other vehicles is likely to see more “impact” events for example.
Many hard-cased packs as also shown in that photo have built-in bullet connectors within the case to accept the main power and balance wiring.
RC air vehicles, however (helicopters, planes, and quad/multi) rotors), generally use soft case RC LiPo batteries.
As shown with the above soft cased LiPo, the cells are simply encased in a lightweight shrink wrap to create the battery pack. There may or may not be a thin, lightweight layer of foam protection also wrapped around the pack before the shrink wrap is applied.
Both power and balance wiring are soldered directly to the cells within the pack further reducing weight and avoiding more failure-prone connection points.
The main advantage to a soft case is obvious – less weight and a smaller form factor as there is no bulky case around the cells.
The other advantages of soft-cased RC LiPo batteries are you can see when they are puffed (which will be covered later on in the article). Hard cased packs, on the other hand, can have puffed cells totally hidden within the case, but the hard case will usually burst when the puffing gets bad enough. LiPo cells enclosed in thin heat shrink also have moderately better heat dissipation over ones that are enclosed in a hard case.
So, for electric-powered RC aircraft, the vast majority of us will use soft-cased LiPo packs for those primary advantageous reasons.
The one “RC aerial discipline” exception I can think of that “bends” this general rule of using only soft LiPo packs is FPV quad-rotor racing.
Those little buggers will often be banging into each other and anything else they fly into that conventional RC pilots want to avoid at all cost.
Just like racing ground vehicles, “some” (certainly not all) FPV racing pilots use hard-cased packs on their racing quads if the quadcopter itself doesn’t protect the LiPo battery pack well.
RC LiPo Battery Ratings
Now that I have bored you to death with LiPo RC battery basics, time to get into the main topics at hand.
First, are the 4 main rating numbers you will see on the Li-Po battery:
Voltage
Capacity
Charge Rate
Discharge Rate
RC LiPo Battery Rating Numbers
Typical RC LiPo Battery Rating Numbers
-
Cell Count / Nominal Voltage
Unlike conventional NiCad or NiMH battery cells that have a nominal voltage of 1.2 volts per cell, LiPo battery cells have a nominal voltage of 3.7 volts per cell.
The benefit here is fewer cells can be used to make up a battery pack and in some cases on smaller micro-sized RC aircraft like most toy helicopters or hobby grade micros like the Blade mCX2, or Nano QX; a single 3.7 volt LiPo cell is all that is needed to power the motor and electronics.
Quickly – What the hell is “nominal voltage”?
Nominal voltage is usually referred to as the “resting voltage” of the battery cell or battery pack. There are exceptions of course in this determination.
Nominal resting voltage is an industry-standard (agreed convention) that varies for all battery chemistry types; but for our RC LiPo chemistry, the usual nominal voltage standard given is 3.7 volts per cell.
That voltage, however, is not the fully charged voltage of the cell (which is as high as 4.2V), nor is it the 50% storage voltage (3.85V), or even the 80% discharged state resting voltage (apx. 3.75V).
This will all be covered in detail throughout my LiPo article, but nominal voltage numbers often confuse folks and I get a fair number of related questions. To keep things simple, just think of 3.7 volts as the guide number used to determine the voltage value you see printed on the LiPo battery pack sticker.
Other than the smallest of electric RC models, RC LiPo battery packs will have at least two or more cells hooked up in series to provide higher voltages. For larger RC models that number can be as high as 6 cells and even more for larger birds or HV (high voltage) applications.
Here is a list of LiPo RC battery pack “nominal” voltages with cell counts. If you are wondering what the 1-14S in parenthesis means; it’s the way battery manufacturers indicate how my cells hooked in series(S) the battery pack contains. Fully charged voltage of the packs is the number in green.
3.7 volt battery = 1 cell x 3.7 volts (1S) 4.2V
7.4 volt battery = 2 cells x 3.7 volts (2S) 8.4V
11.1 volt battery = 3 cells x 3.7 volts (3S) 12.6V
14.8 volt battery = 4 cells x 3.7 volts (4S) 16.8V
18.5 volt battery = 5 cells x 3.7 volts (5S) 21.0V
22.2 volt battery = 6 cells x 3.7 volts (6S) 25.2V
29.6 volt battery = 8 cells x 3.7 volts (8S) 33.6V
37.0 volt battery = 10 cells x 3.7 volts (10S) 42.0V
44.4 volt battery = 12 cells x 3.7 volts (12S) 50.4V
51.8 volt battery = 14 cells x 3.7 volts (14S) 58.8V
I should point out you may run across packs or cells hooked up in parallel to increase the capacity. This is indicated by a number followed by a “P”. Example: 2S2P would indicate two, two-celled series packs hooked up in parallel to double the capacity (2S2P is actually a popular configuration in high capacity LiPo receiver packs).
So, those are the voltages you need to know and each RC model or more specifically, the motor/speed controller combination will indicate what voltage is required for correct operation/RPM.
This number has to be followed to the letter in most cases since a change in voltage equates to a change in RPM and will require changing the gearing but more likely the motor to a higher or lower KV rating – not something I want to get into in this write-up (I cover it in my setup & tips eBook). If a model calls for a 3 cell (3S) 11.1-volt battery – let’s just say that is what has to be used.
A quick word on motor ratings…
Many people new to electric flight get confused by brushless electric motor ratings, specifically the Kv rating thinking Kv = kilo-volts (1 kV = 1000 volts).
This is not the case at all. The Kv rating of a brushless motor refers to the motor’s velocity constant (thus the v). Motors also have a torque constant (Kt value), and a motor constant (Km value); but Kv is the one that is listed and most commonly referenced in RC brushless motor ratings.
Now, this is where the can of Kv worms starts getting really messy and complicated! I’m going to be giving you the easy-to-understand (but wrong) common description. Kv when it comes to brushless motors references a ratio of how many RPM (rotations per minute) it turns per Volt you supply it with.
An example might be something like a 1000 Kv motor with a voltage range of 10 – 25 volts. That would mean this motor will turn at about 10,000 RPM @ 10 volts up to around 25,000 RPM @ 25 volts.
As I said, this RPM per volt idea is wrong but is easy for most people to understand and it actually gets you pretty close to how fast a brushless motor will spin at full power, unloaded, with a specific voltage LiPo pack.
If you want to understand the correct Kv constant relationship, it’s not about how many RPM’s the motor will turn per volt, but rather how much back emf voltage is created while the motor turns. When you spin a motor it creates a voltage, that’s how generators and alternators work after all.
A 1000 Kv rated motor, for example, will generate a 1 Volt back emf when the motor is rotating at 1000 RPM. At 15,000 RPM, this motor will generate 15 Volts.
I don’t want to start into motor ratings; battery ratings are plenty to get through but wanted to clear that Kv question up since I get it so often.
-
Capacity
Capacity indicates how much power/energy the battery pack can hold and is indicated in milliamp hours (mAh), at least on our smaller RC packs. This is just the standard way of saying how much load or drain (measured in milliamps) you can put on your battery for 1 hour at which time the battery will be fully discharged.
For example, an RC LiPo battery that is rated at 1000 mAh would be completely discharged in one hour with a 1000 milliamp load placed on it.
If this same battery had a 500 milliamp load placed on it, it would take 2 hours to drain down. If the load was increased to around 15,000 milliamps (15 Amps); a very common current drain in a 3S powered 450 sized RC helicopter while hovering – the time to drain the battery would be only about 4 minutes.
Note, as the discharge rate increases, the capacity of a battery actually becomes less than stated due to efficiency losses; but in our discussion here, we are keeping things simple and “linear” 🙂
As you can imagine for an RC model helicopter with that kind of current draw, it would be very advantageous to use a larger capacity battery pack such as a 2000 mAh pack. This larger pack used with a 15 amp draw would double the flight time to about 8 minutes. It’s not quite that simple, and there are other considerations to be aware of which will be covered, but you get the idea.
The main thing to get out of this is if you want more flight time; increase the capacity of your battery pack.
RC LiPo Battery Capacity Cell Size Comparison
Unlike voltage, capacity can be changed around to give you more or less flight time.
Naturally, because of size & weight restrictions, you have to stay within a certain battery capacity range seeing that the more capacity a battery pack has, the larger and heavier it will be.
Think of increasing the RC Lipo battery capacity similar to putting a larger fuel tank in the RC vehicle.
-
Maximum Charge Rate
This is the highest charge current rating the manufacturer states the battery can be charged at safely.
A 5C charge rate as shown on our example battery would mean you can safely charge that battery at 5 times its capacity. With that 5300 mAh pack example above, the calculation is 5 x 5300 mA = 26,500 mA or 26.5 Amps – huge!
Please note, however, charging at maximum rates will shorten battery life as is discussed further down this page in the LiPo charging calculation section. This is a safe maximum number, not a best for maximum life number in other words.
Lower charge rates are always better for increasing LiPo battery life!
-
Discharge Rate
This one is probably the single most overrated & misunderstood of all battery ratings.
The discharge rate is simply how fast a battery can be discharged safely while remaining healthy.
Remember that ion exchange thing further up the page? Well the faster the ions can flow from anode to cathode in a battery will indicate the discharge rate.
A battery with a discharge rating of 10C would mean you could & safely discharge it at a rate 10 times more than the capacity of the pack, a 15C pack = 15 times more, a 20C pack = 20 times more, and so on.
Using our 1000 mAh battery as an example; if it has a 20C discharge rating, that would mean you could pull a maximum sustained load up to 20,000 milliamps or 20 amps off that battery (20 x 1000 milliamps = 20,000 milliamps or 20 amps).
From a purely theoretical time standpoint, this equals 333 mAh of draw per minute so the 1000 mAh pack would be completely exhausted in about 3 minutes if it’s exposed to the maximum rated 20C discharge rate the entire time.
Calculation as follows: 20,000 mA divided by 60 minutes = 333 mAh which is then divided into the 1000 mAh capacity of the pack giving us 3.00 minutes).
Most RC LiPo Battery packs will show the continuous C rating and usually a maximum burst C rating as well. A burst rating indicates the battery discharge rate for short bursts (a few seconds maximum) of extended power. An example might be something like “Discharge rate = 25C Continuous/50C Bursts”.
The higher the C rating, usually the more expensive and even slightly heavier the battery gets. This is where you can save some money, and maybe even a little weight.
Getting an extremely high discharge rated pack when there is no way you could possibly pull the full amount of power is not required but it won’t hurt either.
The most important thing is you can’t go with too low a discharge C rating or you will damage your battery and possibly your ESC (electronic speed control).
Just like the maximum charge number, the maximum discharge number is what the manufacturer deems is safely possible, but not at all what will give you the best life.
So how do you know what C rating to get when purchasing your LiPo RC Battery Pack?
The easy answer most will give is to get the largest C rating you can… If money is not an object I agree with that almost 100%.
However, for beginners & intermediate or scale fliers who won’t be performing power hungry 3D maneuvers and drawing much current; stretching your RC battery budget by purchasing lower C rated packs when you’re first learning so you can get a few extra packs makes more sense in my opinion.
Same goes for multi/quad-rotors as they generally don’t pull as much current so lower C rated packs are often used with them as well.
As a very general guideline, 25C to 35C discharge rated packs are the norm for most 150-550 size electric helicopters with general to light sport flying in mind. For larger birds, 30C to 40C discharge rated packs are a safe bet (again for normal to light sport). Once up to aggressive sport or 3D, that is where the 40C and up discharge rated packs come into play.
All this said, Li-Po packs are coming down in price all the time. If you find a 35C pack for the same price as a 25C when that is all you need, go for the 35C pack – it should run cooler and have a longer life span. Like most things, pushing a Lipo pack hard close to its limits will wear it out and reduce its overall lifespan (by a large degree in some cases).
If however you get a pack with a C discharge rating at least double of the maximum you intend to pull out of it; with proper care, there’s no reason you shouldn’t be able to get 300 charge and discharge cycles out of it with average degradation.
As an example, suppose your helicopter uses a motor and ESC both rated at a maximum of 100 Amps, and it uses a 4000 mAh (4 Ah) battery. What C rating should be considered using my double method?
100 Amps / 4 Amps = 25C. Double that = 50C.
Now, in the real world, it’s very unlikely you will be flying and pulling 100 Amps out of your bird all the time. It might only see short bursts of 100 Amps for example in which case that 50C number would be a good burst number to go by, with perhaps a 25C to 30C rating for normal usage.
Again, it depends on how hard you fly/drive.
One interesting point I should mention about selecting discharge ratings seeing that HV (high voltage) electric RC aircraft (usually defined as using Li-Po packs over 8S) are becoming more and more commonplace is the reduced current that HV provides. This, of course, is another topic, but for many HV applications, you can get away with lower C ratings since the models won’t pull as much current as a similar size/powered model running on a lower voltage pack.
The flip side, of course, is most folks who are running HV birds are also pushing them to the limits and will still need high discharge rates… I just wanted to point out why higher voltage can be advantageous (more voltage = less current = less heat).
Using Pack Temperature To Gauge Discharge C Rating
Lastly, taking a temperature reading of your packs after running them is another good way to gauge if you’re using a high enough C rating. I’m afraid to say it, but just because a pack says it is rated at 30C doesn’t necessary mean it is in real-world applications.
Realistically, C ratings are somewhat meaningless because they are not verifiable. On top of that, as packs age, their internal resistance increases which lowers the C rating and makes them run warmer.
The general rule is if you can’t comfortably hold a LiPo pack tightly in your hand after using it, it’s way too hot! This equates to anything higher than about 50C (122F).
That is even way too warm as far as I’m concerned. Nothing higher than 40C (about 104F) is what I consider safe and I rarely have my packs go much past 35C (95F) unless it’s also very hot outside as well. So, if you find your packs are getting warmer than this, it’s a good bet you should consider moving up to a higher discharge rating for your next LiPo pack/s.
Leaving your packs in the car on a hot sunny day can certainly heat them up well past 40C as well. Internal or external heat – both have the same negative effect, hot LiPo’s are miserable and they won’t last long.
The source from https://www.rchelicopterfun.com/lipo-batteries.html